As global demand for livestock feed and sustainable biomass fuels grows, the role of alfalfa pellet making machines has become more prominent in agriculture and industrial operations. While traditional pellet mills are effective, modern operations are increasingly integrating automation and smart technologies to streamline production, reduce labor costs, and improve pellet quality.
In this article, we explore how the incorporation of automation, sensors, IoT (Internet of Things), and AI into alfalfa pellet making machines can dramatically enhance efficiency, reduce downtime, and improve overall output quality.
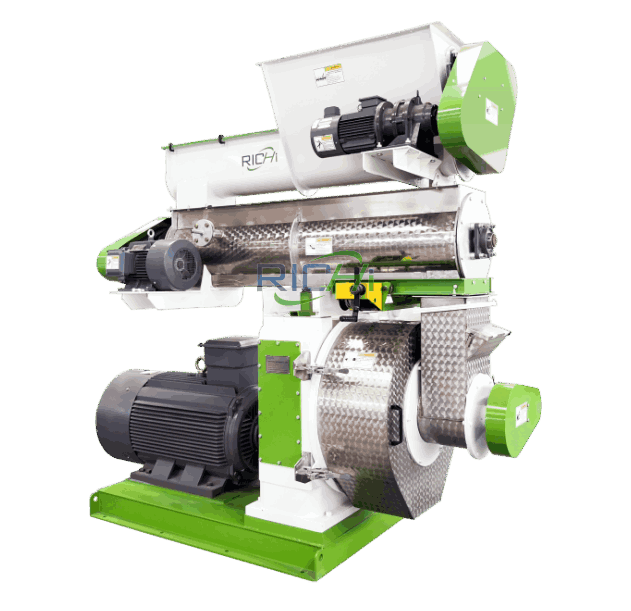
1. The Rise of Automation in Alfalfa Pellet Production
Automation refers to the use of control systems and machinery to operate processes with minimal human intervention. In alfalfa pellet production, automation plays a key role in:
- Maintaining consistent pellet size and density
- Reducing manual labor requirements
- Minimizing operational errors
- Improving data collection and process control
Automated systems can now manage the entire production cycle — from raw material intake to pellet packaging.
2. Key Components of an Automated Alfalfa Pellet Plant
A. Automated Feeding and Dosing Systems
Sensors and programmable logic controllers (PLCs) monitor the input of alfalfa material, ensuring:
- Consistent feeding rates
- Proper moisture control
- Prevention of machine blockages due to overfeeding
These systems adjust automatically to material characteristics such as density and moisture content.
B. Intelligent Moisture Control
Moisture content is one of the most critical parameters in pellet production. Too wet and the pellets won’t bind; too dry and they may crumble or burn.
Smart alfalfa pellet machines now include:
- Infrared or microwave moisture sensors
- Real-time drying system adjustments
- Automated water spraying or steam injection to maintain ideal levels (typically 12–15%) (Related post: Grass Pellet Machine)
C. Adaptive Pellet Mill Operation
Smart machines automatically adjust:
- Roller pressure
- Die rotation speed
- Compression ratios
This ensures optimized compression based on input material conditions, resulting in uniform, high-density pellets.
D. Integration with Cooling, Sieving, and Packing Lines
Automated production lines also include:
- Pellet coolers with temperature and humidity sensors
- Vibrating sieves that remove dust or unformed pellets
- Packaging systems with auto-weighing and sealing capabilities
This end-to-end automation minimizes human error and reduces labor costs.
3. Internet of Things (IoT) in Pelletizing Equipment
IoT allows machines to communicate and share data across networks. In alfalfa pellet mills, IoT is used for:
- Remote monitoring of equipment performance
- Real-time alerts on temperature, humidity, motor load, or blockages
- Preventive maintenance notifications
- Cloud-based analytics to track production trends and inefficiencies
Operators can access dashboards from smartphones, tablets, or PCs — even offsite.
4. AI-Driven Optimization in Alfalfa Pellet Machines
Artificial intelligence (AI) enables machines to learn from data and optimize operations autonomously.
Applications include:
- Predictive maintenance – AI algorithms analyze vibration, temperature, and motor load data to detect upcoming failures.
- Quality control – Computer vision systems scan pellets for shape and size consistency.
- Process tuning – AI adjusts machine settings to maintain optimal energy efficiency and output based on historical performance.
By learning from historical data, AI improves decision-making and reduces the need for manual intervention.
5. Benefits of Automation and Smart Technology Integration
Benefit | Impact on Alfalfa Pellet Production |
---|---|
Increased Productivity | Faster throughput with fewer production delays |
Improved Pellet Consistency | Reduced variation in size, density, and moisture |
Lower Operating Costs | Reduced labor and energy usage |
Enhanced Safety | Fewer manual interventions in dangerous zones |
Predictive Maintenance | Fewer unexpected breakdowns and lower repair costs |
Data-Driven Decisions | Better planning and continuous process improvement |
6. Real-World Example: A Smart Alfalfa Pelletizing Plant
Let’s consider a mid-sized operation in the Midwest U.S. that upgraded its manual alfalfa pelletizing system to a smart, automated line.
Before Automation:
- 6 workers per shift
- Daily output: 12 tons
- 3 hours of average downtime/week
- Frequent moisture-related pellet failures
After Automation:
- 2 workers per shift
- Daily output: 18 tons (+50%)
- Downtime reduced to 30 minutes/week
- Pellet rejection rate dropped by 80%
- ROI realized within 15 months
This transformation was enabled by PLC control, integrated sensors, predictive analytics, and cloud dashboards. (Related project: 15-20T/H Grass Alfalfa Pellet Production Line in USA)
7. Challenges in Implementing Automation
While the benefits are clear, implementing automation comes with challenges:
- Initial capital investment: Higher cost of smart machinery and control systems
- Training requirements: Staff must learn how to operate and interpret automated systems
- Integration complexity: Legacy systems may not be compatible
- Maintenance of sensors and software: Requires skilled personnel
However, long-term savings and performance gains typically outweigh these challenges.
8. Choosing the Right Automated Alfalfa Pellet Machine
When selecting an advanced pellet machine, consider:
Feature | Why It Matters |
---|---|
PLC with touchscreen interface | Easy operation and real-time feedback |
Remote access and IoT support | Enables offsite monitoring and control |
Auto moisture control system | Ensures pellet quality under changing input conditions |
Modular design | Allows upgrades without full machine replacement |
AI-enhanced tuning options | Boosts efficiency by adjusting parameters automatically |
Work with manufacturers that provide training, support, and customizable automation packages.
9. The Future of Smart Pellet Production
Emerging technologies continue to push boundaries. Expect to see:
- Blockchain integration – Ensuring traceability of pellet batches
- Robotics – Automated handling of bales and pellet bags
- Augmented reality (AR) – Remote maintenance and training using smart glasses
- 5G connectivity – Real-time cloud syncing for multi-site operations
These advances will make alfalfa pellet plants more intelligent, flexible, and profitable.
10. Conclusion
Automation and smart technologies are transforming alfalfa pellet production by increasing efficiency, improving quality, and lowering costs. Whether you operate a small farm or a large feed manufacturing facility, embracing modern pelletizing technology offers significant competitive advantages.
With the right planning, equipment selection, and staff training, automation can help future-proof your operations and maximize the profitability of your alfalfa pellet production line.