Fish feed extrusion is a crucial procedure that plays a important role in producing high-grade feed for fish and also various other water pets. The extrusion process can be enhanced by considering several aspects, consisting of component option, process specifications, as well as tracking equipment.
The initial step in enhancing the performance of a fish feed extruder is to thoroughly pick the active ingredients. The best active ingredients will offer the necessary nutrients in the suitable total up to meet the dietary demands of the target varieties. The active ingredients need to be formulated to make certain that they are compatible with the extrusion process as well as will produce pellets or other forms that are consistent in size, form, and structure. The healthy protein as well as fat content of the active ingredients should additionally be very carefully balanced to prevent processing problems.
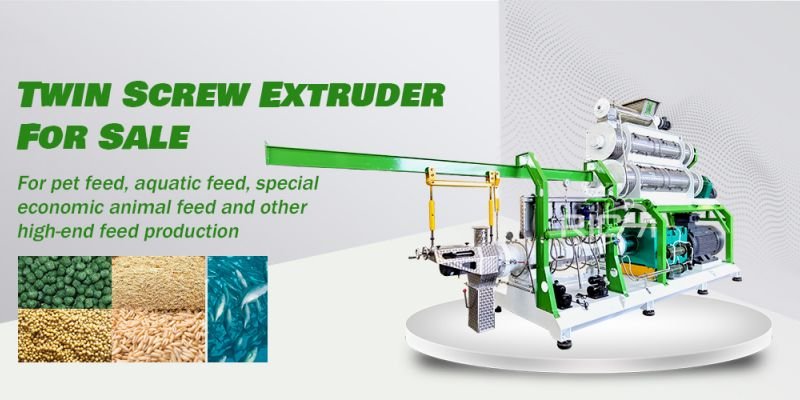
Related post: floating fish feed machine
When the ingredients have actually been picked, the process specifications have to be gotten used to enhance efficiency. Temperature level is among one of the most important process parameters in fish feed extrusion. The temperature in the extruder must be very carefully managed to ensure that the active ingredients are correctly prepared which the pellets are totally formed and also constant in structure. Extreme warm can likewise bring about nutrition loss and also other handling problems. Therefore, it is essential to keep an eye on as well as adjust the temperature throughout the extrusion procedure to achieve optimal outcomes.
Pressure is another important procedure parameter that must be monitored as well as gotten used to optimize efficiency. The pressure in the extruder should be thoroughly regulated to make certain that the ingredients are effectively mixed which the pellets are consistent in size, form, as well as texture. Excessive pressure can likewise bring about processing difficulties and result in pellets that are also hard or dense.Therefore, it is important to very carefully monitor and readjust the stress in the extruder to accomplish the wanted outcomes.
Along with adjusting process criteria, checking the extruder for uniformity as well as high quality is additionally crucial in optimizing efficiency. Regular screening and also monitoring can help determine potential issues prior to they come to be considerable troubles, permitting producers to make modifications and boost the total high quality of the end product.
Sensing units and also checking equipment can be made use of to check the temperature and also stress in the extruder. Temperature level sensors can be utilized to monitor the temperature in the extruder as well as make sure that it stays within the preferred array. In a similar way, stress sensors can be used to keep track of the stress in the extruder and also ensure that it continues to be within the desired array. Normal screening can also help identify concerns with pellet uniformity and also top quality, permitting manufacturers to make changes to the extrusion procedure as required.

Along with active ingredient selection, procedure criterion modification, and surveillance equipment, other factors can additionally impact the performance of a fish feed extruder. Upkeep as well as cleansing of the extruder are crucial in making sure that it runs at peak performance. Regular cleansing can aid prevent accumulation and blockages that can result in refining difficulties.
Finally, optimizing the efficiency of a fish feed extruder calls for cautious consideration of a number of variables, consisting of active ingredient selection, process specification adjustment, and also surveillance devices. By picking the right active ingredients, changing process criteria, and keeping track of the extruder for consistency as well as top quality, producers can accomplish the very best possible results and create top quality, nutritionally total feed for fish and also other water pets. (Follow RICHI on Facebook)